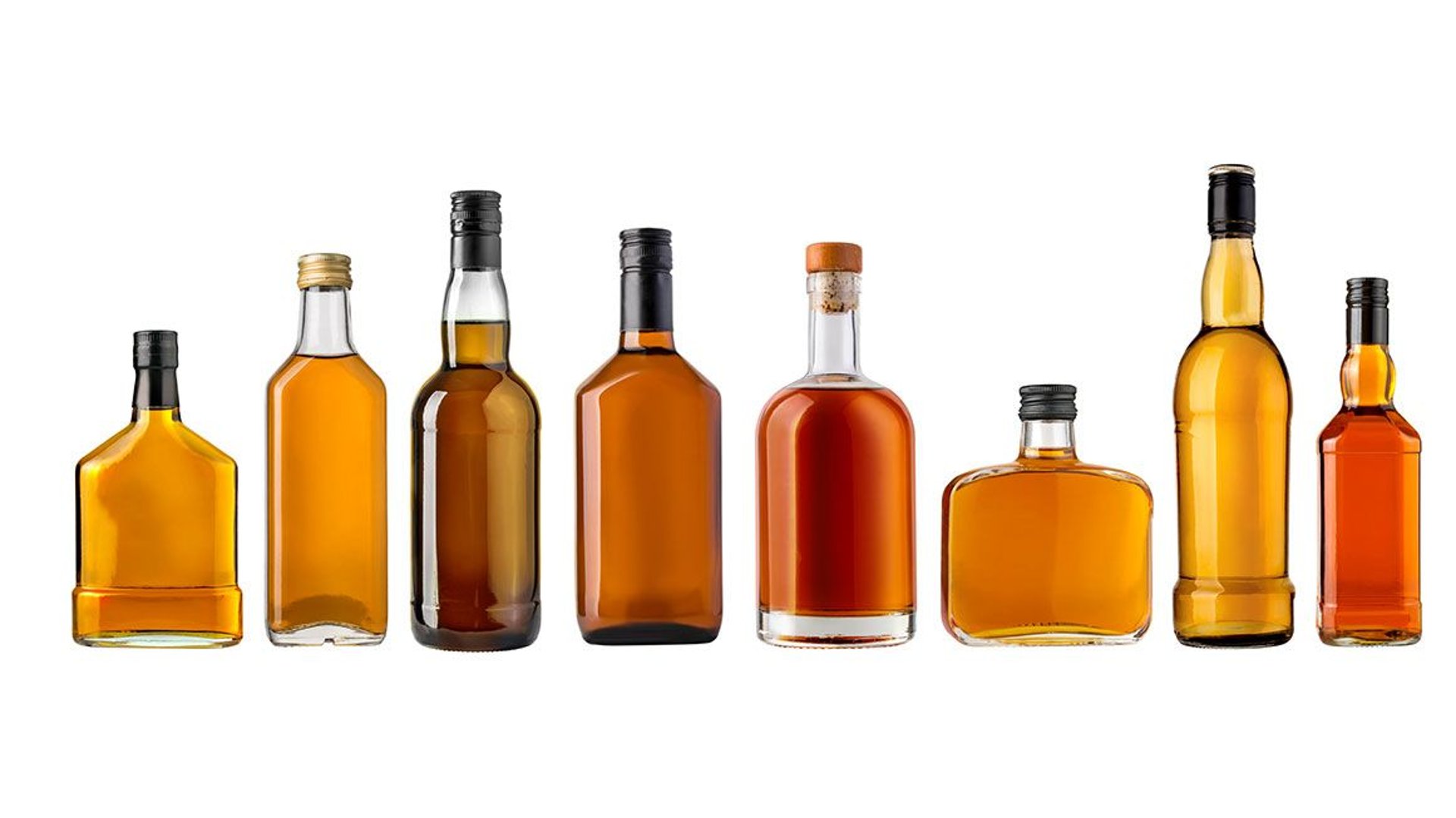
Tequila Bottle Manufacturer
we design and produce vibrant and unique glass bottles that capture the lively essence of tequila. Our bottles are crafted to enhance the visual appeal and showcase the rich tradition and craftsmanship behind your tequila. Available in various shapes and sizes, our bottles are perfect for presenting both premium and artisanal tequilas with style and elegance.
High-Quality Material: Lead-free high flint glass for exceptional clarity and strength.
Distinctive Designs: A variety of shapes and sizes to reflect the lively spirit and tradition of tequila.
Superior Sealing: Options include corks, screw caps, and Guala caps to maintain freshness and flavor.
Customization: Personalized bottle shapes, colors, and labels to match your brand’s unique identity.
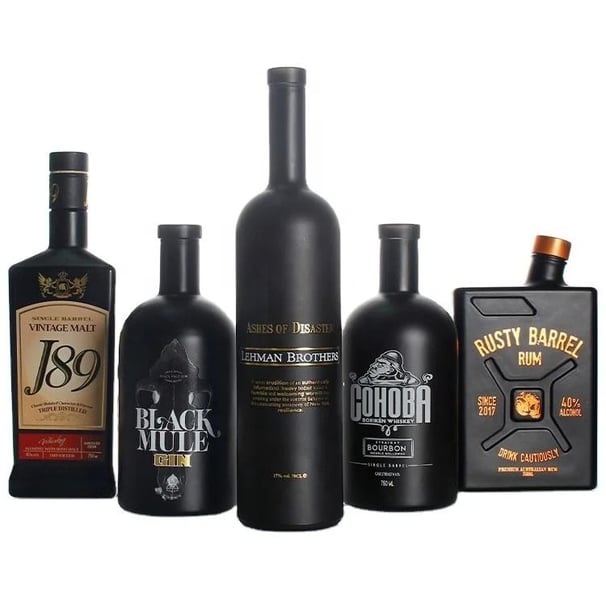
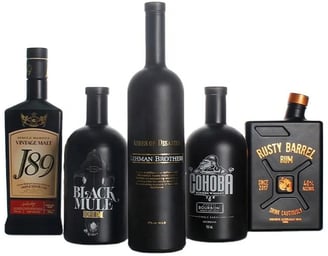
Our tequila bottles are made from high-quality, lead-free high flint glass, ensuring durability and clarity. These bottles are designed to highlight the vibrant colors and unique qualities of your tequila, making them a standout choice for any occasion.
Tequila Bottles Details
We understand that every tequila brand has unique needs. Our customization services include:
Bottle Shape and Size: Choose from classic round bottles, square bottles, and unique custom shapes.
Color Options: Available in transparent, amber, and other custom colors to suit your branding.
Label Design: Personalized label printing and embossing options to enhance your brand’s visual appeal.
MOQ: 6000 pieces
Bottle Capacity: Available in 500ml, 700ml, 750ml, and 1-liter sizes
Material: Lead-Free High Flint Glass
Bottle Shapes: Round, Square, Custom Designs
Color: Transparent, Amber, Custom Colors
Stoppers: Cork, Screw Cap, Guala Cap
Application: Suitable for aged whiskey, blended whiskey, bourbon, and other spirits
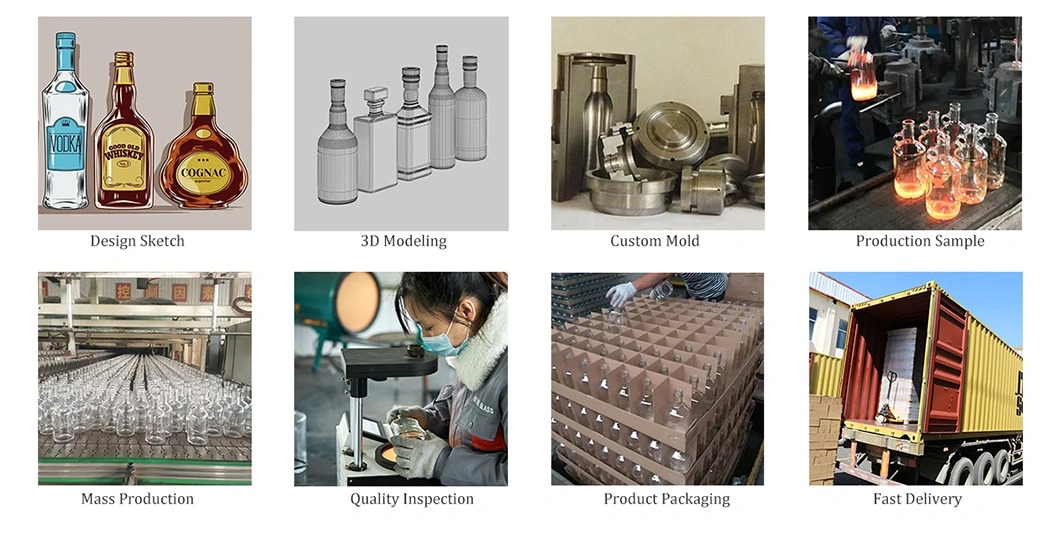
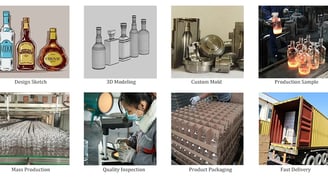
Design Sketch: Our expert designers create detailed sketches based on your specifications and branding requirements, ensuring the perfect shape and aesthetic for your whiskey bottle.
3D Modeling: We use advanced software to transform sketches into 3D models, allowing for adjustments and ensuring the final product meets your expectations.
Custom Mold: We create a custom mold from the finalized design, ensuring each bottle meets exact specifications and maintains high quality.
Production Sample: A sample bottle is produced from the custom mold for your review, ensuring it meets your standards before mass production.
Mass Production: Upon sample approval, we proceed with mass production in our state-of-the-art facility, maintaining the highest quality standards.
Quality Inspection: Each batch undergoes rigorous inspections for consistency in shape, clarity, and durability, ensuring every bottle is perfect.
Product Packaging: Bottles are carefully packaged to prevent damage during transit, using high-quality materials to ensure they arrive in perfect condition.
Fast Delivery: We partner with reliable logistics companies to ensure fast and safe delivery, both locally and internationally.
Bottle Decoration
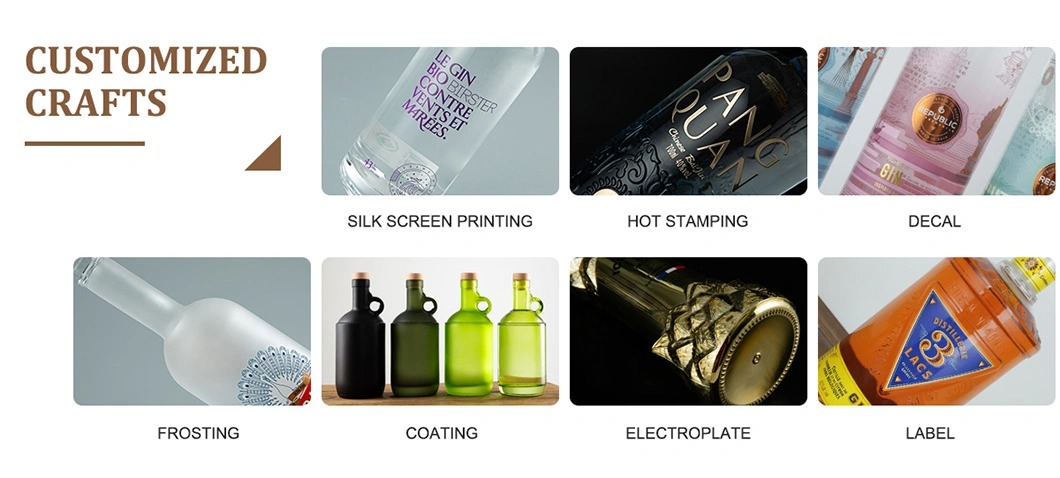
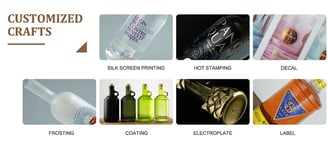
Frosting
Enhance the look and feel of your bottles with a frosted finish, giving them a premium, matte appearance.
Silk Screen Printing
Add intricate designs and logos directly onto the bottle with durable and vibrant silk screen printing.
Coating
Apply a protective coating to your bottles for added durability and a glossy finish.
Hot Stamping
Achieve a luxurious look with hot stamping, adding metallic accents to your bottle design.
Electroplate
Create a striking metallic finish on your bottles with electroplating, perfect for a modern, high-end appearance.
Decal
Customize your bottles with detailed and colorful decals for a unique, branded look.
Label
Add custom labels to your bottles for clear branding and information display, available in various shapes and materials.
Quality Control
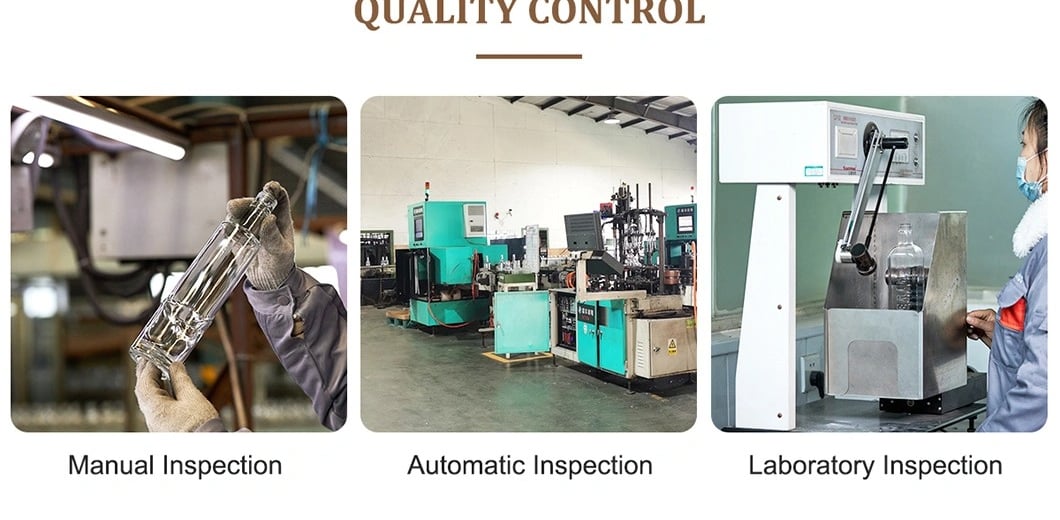
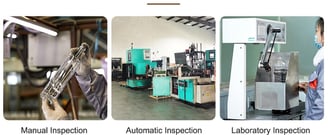
Quality Assurance
Quality is at the core of our manufacturing process. We implement stringent quality control measures at every stage of production. Our quality assurance team conducts rigorous tests to ensure each bottle meets our high standards of durability, safety, and appearance.
Resistance to Internal Pressure Tester
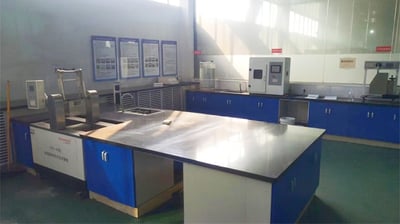
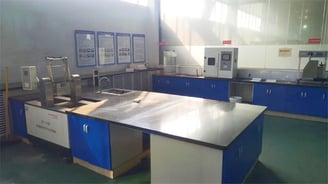
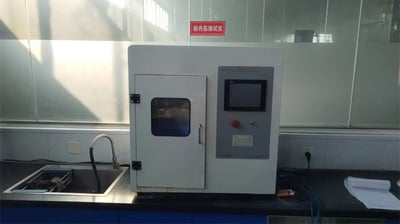
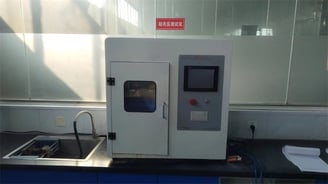
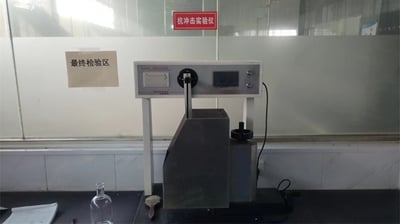
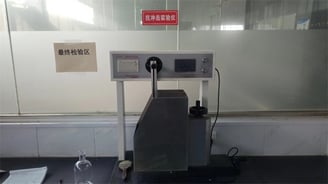
Compressive Stress Tester

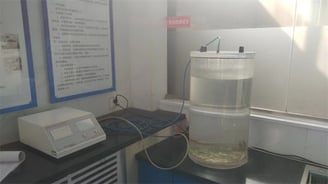
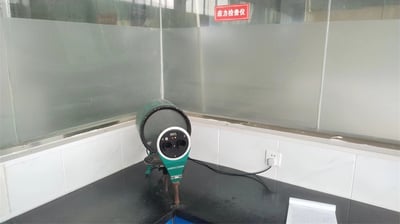
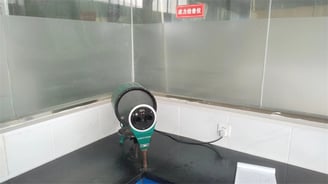
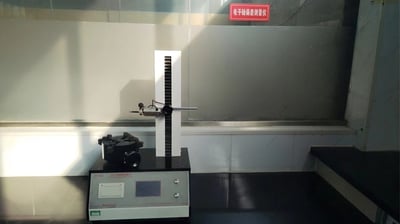
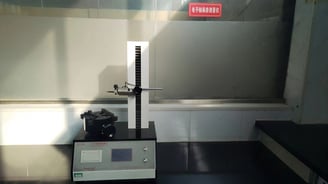
Testing Center
Impact Resilience Tester
Electronic Bottom Thickness & Wall Thickness Measuring Instrument
Electronic Shaft Deviation Measuring Instrument
Absolutely thrilled with my purchase! Outstanding product, exceptional service, and overall an excellent buying experience.
Clarice Turner
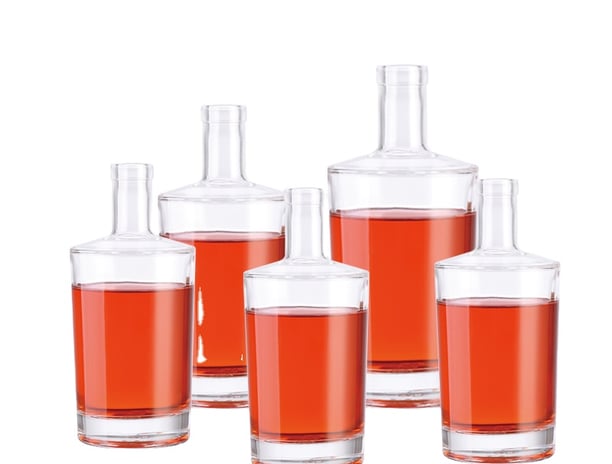
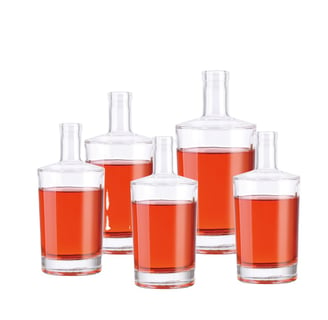
★★★★★
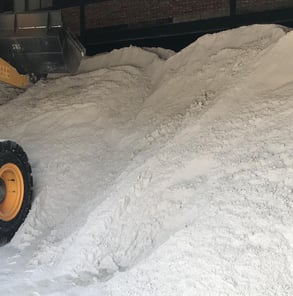
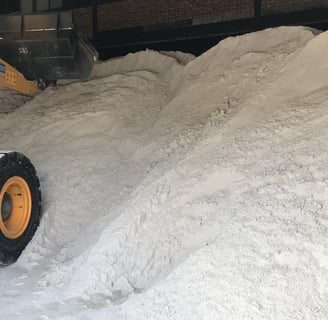
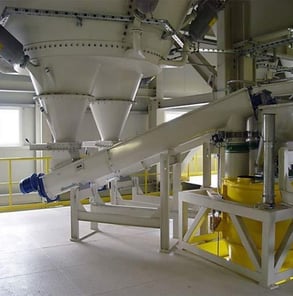

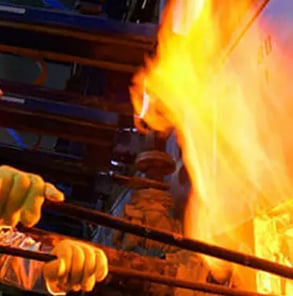
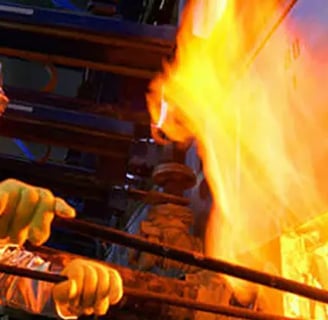
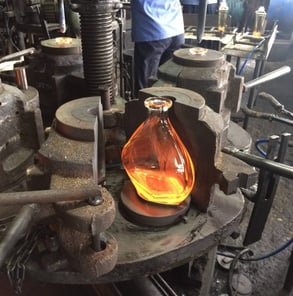
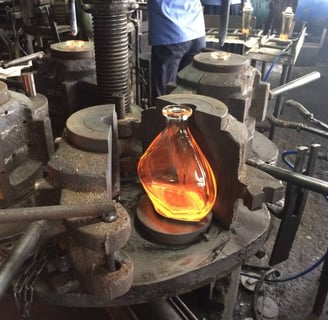
1.Choosing the raw material
Glass bottle manufacturing starts with selecting raw materials, typically 7 to 12 types including silica sand, sodium carbonate, and limestone. Silica is crucial for strength and its quantity varies based on glass type, influencing melting points.
2.Batch house
In the batch house, raw materials are continuously weighed, mixed, and fed into the furnace. A magnet on the conveyor belt removes any magnetic materials. Consistent composition is maintained throughout the process.
3.Melting
During melting, batched materials are heated in the furnace to temperatures ranging from 1550 to 1600 degrees Celsius, forming uniform, bubble-free liquid glass meeting molding standards. Melting temperature varies with composition.
4.Feeding
In the feeding stage, glass gob is fed to glassblowers at optimal temperatures determined by bottle weight and shape. It's then fed into the forming machine through feeders equipped with adjustable openings controlled by low shear panels. Sheer speed control adjusts for different glass sizes.
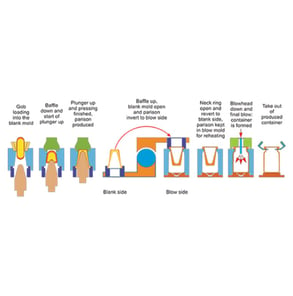
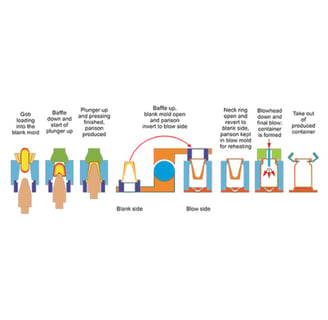

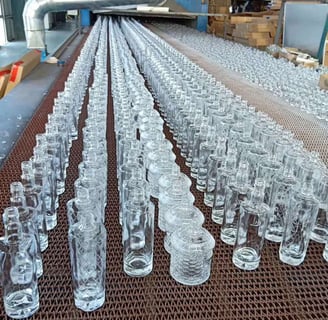
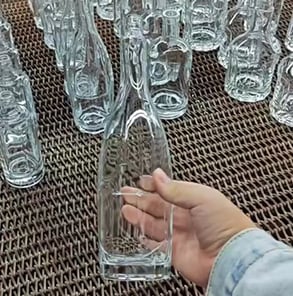
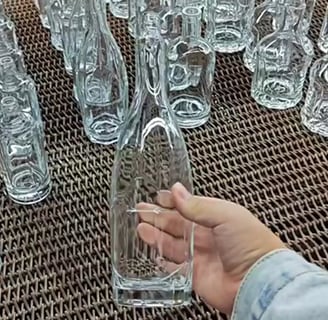
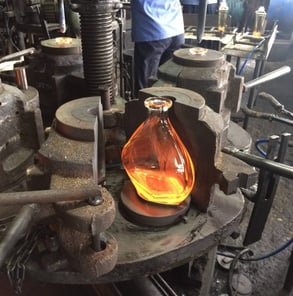
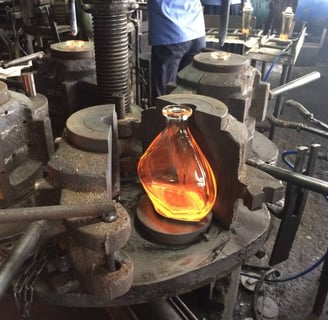
5.Forming
After the elongated shape is cut from the furnace, it is transferred into a mold by the forming machine. Air is blown into the mold to shape the glass. Once the bottle shape is formed, it is removed from the mold. Any additional shaping or joining must be done before the glass hardens, or it will need to be remelted.
6.Annealing
After the glass is formed, it undergoes annealing to remove stress, phase separation, or crystallization. Rapid cooling of the outer surface compared to the interior causes stress. Annealing cools the glass evenly, preventing cracks and strengthening the bottle.
7.Inspection
After the glass is formed, it undergoes annealing to remove stress, phase separation, or crystallization. Rapid cooling of the outer surface compared to the interior causes stress. Annealing cools the glass evenly, preventing cracks and strengthening the bottle.
8.Packing and Shipment
Based on customer requirements, bottles are packed accordingly. They are wrapped in cardboard boxes with segments separated by corrugated sheets. Packaging is mostly automated to prevent damage. Bottles are then stored in a warehouse or shipped to customers.
Welcome to Alkaglass, your trusted partner for glass bottle manufacturing solutions. We provide extensive customization choices and production services to realize your unique requirements and ideas.